Motor operated valves (MOVs) have become the essential building blocks in automated flow control systems. From oil and gas to water treatment and chemical processing, understanding how valves and actuators work together is crucial for anyone involved in modern pipeline or industrial automation. This comprehensive guide covers every key point about MOVs—including valve types, working principles, actuator selection, maintenance, and real-world application cases. Whether you’re an engineer, maintenance manager, or OEM, this article will help you make smarter choices, avoid costly mistakes, and achieve precise control over your fluid systems.
1. What Is a Motor Operated Valve (MOV) and Why Do Industrial Systems Need Them?
A motor operated valve (MOV) is a type of valve equipped with an electric actuator to open or close automatically in response to control signals. Unlike manual valves that require direct human operation, MOVs rely on a motorized actuator—often an electric motor—to deliver the necessary torque and movement for valve operation. This combination enables valves and actuators to be deployed in pipelines and process systems where remote operation, safety, and repeatability are essential.
Why are MOVs critical in modern industry?
- Remote and automated operation: Essential for hard-to-reach or hazardous environments, like power generation and chemical processing plants.
- Consistent and precise control: MOVs enable accurate management of fluid flow, pressure, and temperature, which manual valves simply cannot match.
- Safety and system integration: MOVs can be integrated into distributed control systems (DCS), PLCs, or SCADA, allowing rapid response to emergencies and system changes.
Industry Applications:
MOVs are widely used in applications such as pump discharge, water treatment, power plants, oil and gas pipelines, and HVAC systems. In fact, valves are generally of large diameter and mass in these sectors, making manual operation impractical.
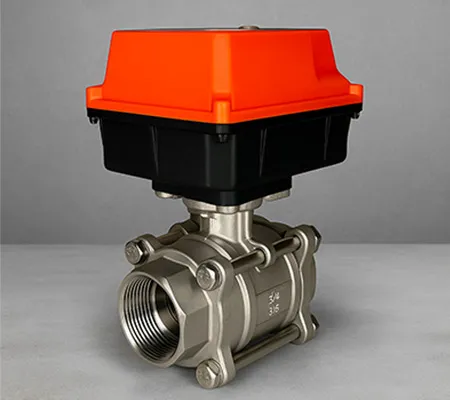
What Is a Motor Operated Valve
For an example of smart valve automation in real-world projects, see our Smart Valve Solutions.
2. How Does a Motorized Valve Work and What Makes It Reliable?
A motorized valve integrates a mechanical valve (such as a ball valve, butterfly valve, plug valve, or gate valve) with an electric actuator. The actuator uses an electric motor to control media flow—translating electrical energy into rotational or linear movement that opens or closes the valve stem.
Basic Operating Principle:
- Control system sends a signal (digital or analog) to the actuator.
- Actuator powers up, delivering torque to turn or lift the valve body.
- Valve moves to the desired position—either fully open, fully closed, or anywhere in between for modulating control.
- In on-off scenarios, the valve simply opens or closes.
- In control valve applications, the actuator can provide precise control to match changing process needs.
Reliability Factors:
- Fail-safe design: Many MOVs include fail-safe mechanisms. For example, in the event of a power failure, spring-return actuators will close the valve or move it to a safe state.
- Durable construction: MOVs are built to handle thousands of cycles, heavy loads, and adverse environments (water, steam, chemical exposure).
- Easy to install: Modern actuators often come with plug-and-play wiring and adaptable mounting, making integration into existing systems simple.
For advanced electric ball valve models and their reliability features, visit our Electric Ball Valve page.
3. What Role Does the Actuator Play in Valve Automation?
The actuator is the engine of any motor operated valve. Its purpose is to actuate the valve—applying sufficient torque to move the valve mechanism. Actuators are designed in several variants:
- Electric actuators (most common for MOVs): Use an electric motor to rotate or lift the valve stem.
- Quarter-turn actuators: Rotate the valve 90°, perfect for ball and butterfly valves.
- Multi-turn actuators: Rotate the stem multiple times, required for gate and globe valves.
Key Features of Electric Actuators:
- Remote operation via digital control systems.
- Modulating capability for continuous valve position control.
- Position feedback: Reports exact valve position back to the control room.
- Manual override: Allows hand operation during maintenance or power loss.
For more about our full line of electric actuators, see Proportional Rotary Actuator.
4. Understanding the Main Types of Motor Operated Valves: Ball, Gate, Globe, Butterfly, Plug
Below is a comparative table summarizing the most common types of motor operated valves and their typical uses:
Valve Type |
Operation Mode |
Typical Application |
Torque Needed |
Standards |
Ball Valve |
Quarter-turn |
On-off, isolation, pump discharge |
Low-Medium |
API 6D |
Butterfly Valve |
Quarter-turn |
Large pipelines, water, HVAC |
Low |
ASME B16.34 |
Gate Valve |
Multi-turn |
Main isolation, water, steam |
High |
API 600 |
Globe Valve |
Multi-turn |
Flow regulation, chemical processing |
Medium-High |
ASME B16.34 |
Plug Valve |
Quarter-turn |
Rapid open/close, special media |
Medium |
API 6D |
Highlights:
- Ball valves and butterfly valves dominate in automation due to simple quarter-turn motion, tight shutoff, and easy maintenance.
- Globe valves and gate valves are used for more precise throttling or full isolation in larger pipelines.
- Plug valves are ideal for applications requiring rapid cycle times or special corrosion resistance.
Learn more about our Electric Butterfly Valve solutions and Plug Valve Applications.
5. Why Should You Motorize Your Valves? Main Benefits in Modern Plants
Why motorize?
Motorizing your valves offers key advantages across various industries including oil and gas, water treatment, power generation, chemical processing, and HVAC. Here’s why so many organizations are moving from manual valves to motor-operated valves:
- Remote operation: No need for operators to access hazardous or remote locations. With a motor operated valve, one click from the control room opens or closes any valve in the plant.
- Automatic control and sequencing: Valves and actuators can be programmed for scheduled or conditional actions, enabling safe and efficient operation of entire systems.
- Precise process control: Motorized valves enable tight regulation of flow rate, temperature, and pressure—vital for maintaining product quality and process safety.
- Reduced labor costs and fewer errors: Manual valves are prone to human error and require more manpower, especially for large or frequently operated valves.
- Integration with smart automation: Modern motorized valves are used as part of smart grids and IoT systems, offering remote monitoring, predictive maintenance, and seamless integration with digital platforms.
Quote:
“In a recent water treatment project, using motorized ball valves reduced emergency shutdown response times from 30 minutes to just 2 minutes—directly contributing to improved safety and uptime.”
— Project Engineer, Water Utility
For more about integrating smart valves into your automation system, check our Smart Water Valve product page.
6. How to Choose the Right Valve Actuator for Your Application
Selecting the correct actuator for your valve is critical to ensure safe, reliable, and efficient operation. Here are the main factors to consider:
Key Selection Criteria:
- Type of valve: Is it a quarter-turn valve (ball, butterfly, or plug valve) or a multi-turn valve (gate, globe)?
- Required torque: Always match the actuator’s torque rating to the size of the valve, pressure, and the media type. Undersized actuators can cause failure to open or close the valve under load.
- Power supply: Do you have access to AC or DC power? Some sites require low-voltage DC actuators for safety, others use 110V/220V AC for convenience.
- Control requirements:
On-off: For simple open/close action.
Modulating: For proportional control (e.g., regulating flow in response to sensor feedback).
Fail-safe needs: Should the valve move to a specific position in the event of a power failure (e.g., close for safety)?
- Environmental conditions: Consider temperature, humidity, explosive atmospheres, or exposure to chemicals.
Table: Example Sizing for Common Motorized Valves
Valve Type |
Typical Size (mm) |
Required Torque (Nm) |
Actuator Type |
Example Application |
Ball Valve |
15–100 |
10–100 |
Electric quarter-turn |
Pump discharge, isolation |
Butterfly Valve |
100–600 |
50–1200 |
Electric quarter-turn |
Water treatment, HVAC |
Globe Valve |
50–200 |
30–300 |
Electric multi-turn |
Chemical dosing |
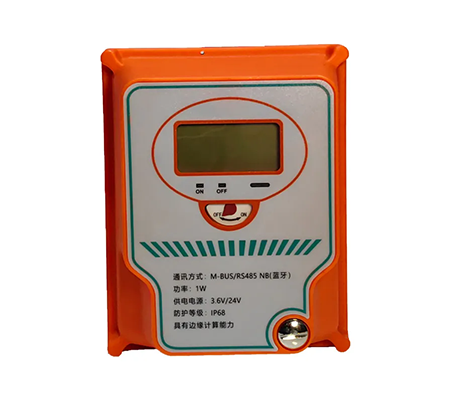
Valve Actuator
Explore actuator sizing options on our Electric Valve Actuator page.
7. On-Off vs. Control Valves: What’s the Difference?
On-Off Valves:
- Designed to be either fully open or fully closed—no intermediate positions.
- Used for isolation, safety shutoff, or simple start/stop control.
- Typical examples: motor operated gate valves, ball valves, and butterfly valves in water supply pipelines.
Control Valves:
- Designed for modulating service—able to hold any position between open and closed.
- Provide precise control of fluid flow, pressure, temperature, or other process variables.
- Typical examples: globe valves, actuated ball valves, and special control valves with feedback signals.
Which to choose?
- Use on-off valves for isolation or emergency shutdown.
- Use control valves where controlling the flow (or other variables) is critical for process quality or safety.
For more details about control valves and their functions, see our Flow Regulating Valve overview.
8. How Ball Valves and Butterfly Valves Transform Automation
Ball Valves:
- Quarter-turn design allows rapid open/close with minimal effort.
- Provides bubble-tight shutoff, making them ideal for on-off control, pump discharge, and safety isolation.
- Actuated ball valves are widely used due to their durability and ability to handle a wide range of fluids—including oil and gas, chemicals, water, and steam.
Butterfly Valves:
- Also a quarter-turn valve, but best suited for large valves and high-flow applications.
- Simple, compact, and lightweight—easy to install and maintain.
- Used in water treatment, power plants, and HVAC systems.
Case Study:
“When a district heating plant in Northern Europe replaced manual butterfly valves with electric actuated valves, they reduced operator workload by 80% and enabled real-time remote monitoring, thanks to integration with their building management system.”
Compare options for Electric Butterfly Valves and Ball Valve Solutions.
9. Installation, Operation, and Maintenance Tips for MOVs
Proper installation and maintenance of motor operated valves (MOVs) and their actuators are vital for ensuring long-term, reliable performance in any piping system.
Installation Tips:
- Alignment: Ensure the actuator is correctly mounted on the valve, with precise alignment to the valve stem. Misalignment increases wear and can cause premature failure.
- Electrical Connections: All wiring must comply with site standards and actuator manufacturer instructions. Use correct voltage for the electric motor.
- Environment: Protect actuators from water, steam, and dust. For outdoor installations or in corrosive atmospheres (such as chemical processing), use weatherproof or explosion-proof actuator housings.
- Pre-Operation Checks: Before bringing the system online, cycle the motorized valve fully open and closed. Verify the actuator reaches all positions smoothly and the feedback system communicates accurately.
Maintenance Tips:
- Routine Inspection: Regularly inspect the actuator and valve body for leaks, corrosion, or signs of damage. Check seals, gaskets, and wiring.
- Lubrication: Moving parts, especially on large valves, may need periodic lubrication as per manufacturer guidelines.
- Testing Fail-Safe Function: If equipped, test fail-safe operation (such as closing the valve during a power failure) to ensure safety in emergencies.
- Manual Override: Train operators to use manual override features safely for open and close in the event of actuator issues.
Stat/Facts:
According to a recent survey, proper installation and scheduled maintenance can extend the operational life of MOVs by up to 40%, significantly reducing downtime in applications such as pump discharge and critical process pipelines.
See our Regulating Valve Function page for best practices on maintaining electric actuated valves.
10. Case Studies: Motorized Valves in Water Treatment and Power Generation
Case 1: Water Treatment Plant (Control of Water and Flow Rate)
A municipal water treatment facility upgraded to motorized valves and electric actuators to manage flow in a complex network of pipelines. By integrating MOVs, the plant achieved:
- Remote valve control for critical treatment stages.
- Precise control of chemical dosing using modulating globe valves.
- Automated isolation using on-off motorized ball valves in emergency shutdowns.
- 25% reduction in manual labor and improved compliance with water safety regulations.
Discover the latest Electric Valve for Water solutions used in water treatment systems.
Case 2: Power Generation Facility (Including Oil and Gas)
A combined-cycle power plant replaced manual gate valves with motor operated valves (MOVs) on steam and water supply lines. Benefits included:
- Automated operation and monitoring from the control room.
- Enhanced safety—automatic valve closure in the event of a power failure or system alarm.
- Compliance with industry standards such as API 6D and ASME B16.34.
- Efficient management of fluid flow and temperature control throughout the plant.
Quote:
“Switching to electric actuated valves reduced our emergency response time and improved plant reliability. The new system seamlessly integrates with our existing DCS and safety protocols.”
— Lead Engineer, Power Generation
Learn more about compliance-ready Electric Valve Actuators.
11. Frequently Asked Questions (FAQ) about MOVs, Actuators, and Control
Q1: What happens if power is lost to a motor operated valve?
A: Most modern MOVs include fail-safe features. For example, a spring-return actuator will automatically close the valve or move it to a predefined safe position in the event of a power failure.
Q2: Can MOVs be used for both on-off and modulating control?
A: Yes, by choosing the right actuator and type of control signal, you can use MOVs for simple open/close or precise control of flow rate and other process variables.
Q3: What standards apply to MOVs and actuators?
A: Industry standards include API 6D for pipeline valves and ASME B16.34 for design and testing of valves. Adhering to these ensures safety and quality.
Q4: Are motorized valves easy to install?
A: Yes, modern designs make them easy to install with standardized mounting and plug-and-play electrical connections.
Q5: What are MOVs typically used for?
A: MOVs are used for different applications such as water treatment, chemical processing, power generation, HVAC, and applications requiring reliable and remote control of large valves.
Internal Link Example:
For more answers on specific valve applications, visit our Smart Valves FAQ.
12. Valve Standards and Compliance: API 6D, ASME B16.34, and More
API 6D and ASME B16.34 are the two main standards that govern valve types and actuator assemblies for industrial pipelines.
- API 6D: Covers design, manufacturing, testing, and documentation for pipeline valves—including ball, plug, and gate valves—used in applications such as oil and gas transmission.
- ASME B16.34: Sets requirements for pressure-temperature ratings, materials, dimensions, and testing for valves used in process piping.
- Other Standards:
- b16.34: Design, materials, and performance of pressure-rated valves.
- Valves from Valworx and other international suppliers also comply with CE, ISO, and local regulations for global deployment.
Fact:
Compliance with recognized valve standards is mandatory for many regulated industries and for ensuring product reliability, especially in safety-critical installations.
Bullet Point Summary: Most Important Things to Remember
- MOVs integrate a mechanical valve and electric actuator for remote, automatic, and precise valve control.
- Choose between on-off or control valves based on your process requirements—modulating actuators allow for precise control of fluid flow and pressure.
- Always match actuator torque and power supply to the size of the valve and expected operating conditions.
- Ball valves and butterfly valves are the most popular motorized valves for automation; plug, gate, and globe valves serve more specialized roles.
- Proper installation, alignment, and maintenance (including fail-safe checks) are critical for safe and reliable operation.
- MOVs and actuators must comply with standards such as API 6D and ASME B16.34 for regulated industries.
- Motorized valve systems are widely used for different applications—from water treatment and chemical processing to power generation and HVAC.
- Take advantage of smart actuators for remote operation, diagnostics, and easy integration with digital control systems.
Further Reading & Related Products:
string(94) "https://www.navarchjncn.com/news/understanding-stainless-steel-ball-valves-the-ultimate-guide/"